Have you ever had to troubleshoot a hydraulic unit problem? You can be a salesman, maintenance person, or service provider, the guidelines to diagnose and fix the problem are the same. In most plants, troubleshooting is through the process of changing industrial parts. This can be expensive in parts costs and downtime if you are not sure what you are doing. When a machine is operational it is not easy to learn the problem. For many random things, people do in the process of fixing the hydraulic issue. Below are steps to follow for effective hydraulic troubleshooting.
1. Know the problem
Hydraulic issues are pressure or volume. If it is pressure, it is not building high enough to operate the machinery properly. Volume could be the problem if the issue is speed-related. Either there is a pass by somewhere in the system or the pump is not delivering the amount of oil required. Challenging hydraulic issues are those that happen intermittently. In such cases, everything appears normal while operating, but it is not steady. And the hydraulics can have some hiccups, and you cannot identify what the issue could be. Such issues need you to do proper research. Since it may be a minor issue, you will notice it when keen. As a first step, always identify the problem to make it easy to fix the issue.
2. Collect information
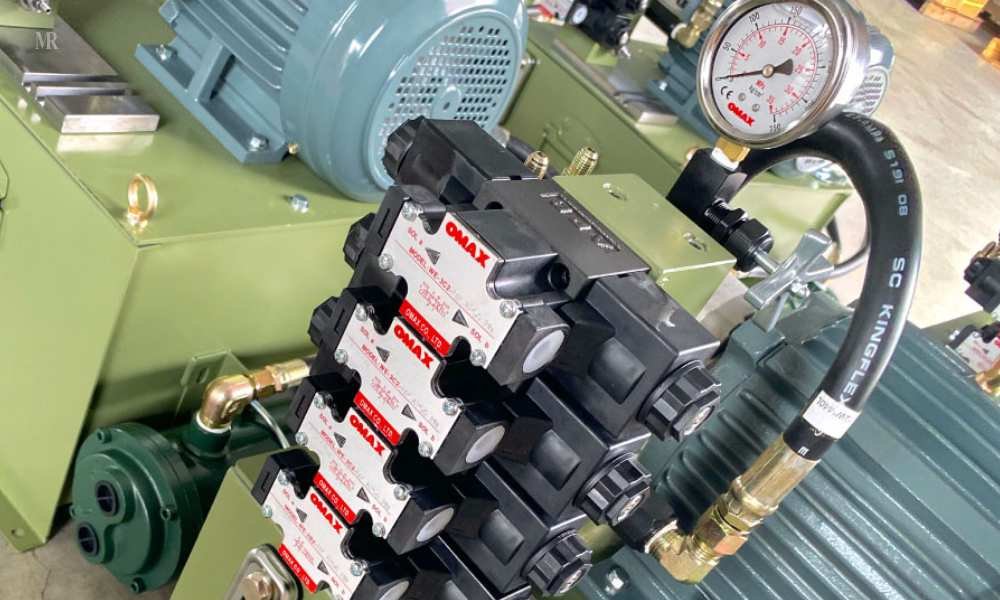
After identifying the issue, the next crucial step is to gather detailed information. By the time you approach a hydraulic system problem, preliminary assessments have often been made. These might pertain to electrical aspects or necessary pressure adjustments. It’s essential to check whether the new components match the part numbers of the ones they’re replacing. Even a minor discrepancy in part numbers can lead to ineffective performance. Hence, confirming the exact part numbers is crucial for the optimal operation of the hydraulic system.
During this information collection phase, conduct thorough visual inspections. Assess the condition of filters, check oil levels, and evaluate pump coupling conditions, looking for any signs of leakage, among other things. It’s essential to closely examine the state of hydraulic hoses too, as wear or damage here can significantly reduce system efficiency. Also, ensure all connections and fittings are securely in place and inspect other components for signs of corrosion or degradation. Regularly checking these elements can prevent significant system failures.
Furthermore, confirm the cleanliness of the oil by reviewing the most recent oil analysis report. Gathering insights from machine operators is also invaluable; they have firsthand knowledge of how the unit should operate generally in terms of sound, feel, and performance. Remember, most maintenance personnel are only called upon when there’s an existing problem with the machine.
3. Review the schematic

While you trace and read the hydraulic schematic, it is the best way to diagnose the issue. Follow the lines on the schematic to find the problem before changing out any part. This will avoid people working on repairing the hydraulic valve while stuck on what the issue could be, do not assume the help of the schematic, as it helps to identify the problem faster than doing it all alone. Also, you save downtimes if you took the time to diagnose the issue from the schematic immediately after the machine went down.
4. System diagnosis and adjustments
After you have done the above steps, you should verify that the system pressures to check their settings. This includes the pressure-reducing valves, pump compensator, relief valve, and other pressure control valves in the hydraulic systems. Since most times, you can solve an issue by setting the pressure at the correct level. As you diagnose the system check accumulators using an infrared camera. When troubleshooting pressure problems, always isolate various points in the system. If there is a pressure problem in the machine, the oil may be bypassing the system.
5. Reliability checklist
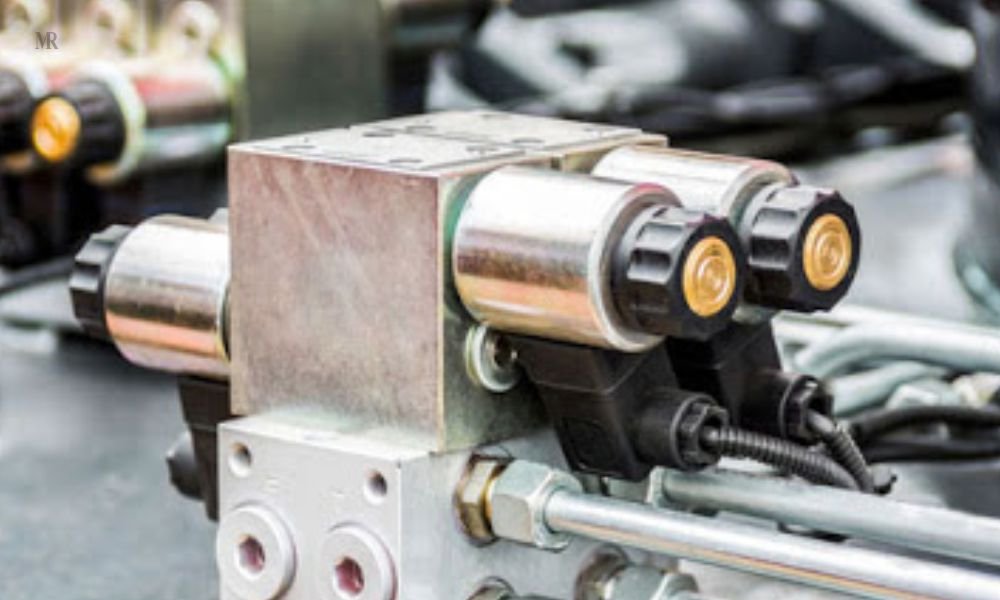
Once you solve the issue, the toolboxes are loaded up, and everyone returns to their duties. What is vital for the future is to develop a reliability checklist on the hydraulic system. The checklist should consist of temperature and pressure readings, oil cleanliness, filter and breather conditions, current readings on the electric motor, conditions of clamps and hoses, voltages to proportional valves, among others. Do this check regularly to avoid unnecessary downtime. In the future, the recorded information will be a great tool in case of any hydraulic issues. When a machine breaks down, most times, the problem is simple, but most people start changing parts. Thus, it is not about only changing parts, but becoming an effective hydraulic system troubleshooter.
Also Read: Coronavirus Hoax: Addressing the pandemic of misinformation